メインボード用ケースを作成 その1
2017.12.05
ABSの反り対策といえば、ヒートベッドを使って底面の温度を上げる。
温度を上げると、その下にあるメインボードが熱せられる。
熱せられるとモータードライバのヒートシンク効率が下がる。
結果、脱調・暴走へと繋がってしまう。
このジレンマのせいで、ベッドの温度を80度までにして
ギリギリ動くラインを見極めているのですが、
印刷終了後、どうしても目視できるレベルの反りができてしまう。
小さいものを印刷して、良くて0.5mm、悪ければ1mmほど角が浮く。
やっぱり100度を超えたいよね。
ということで対策を考えれば
それはもうメインボードを天井に設置か
外に出すことしかありません。
私は、専用ケースを作成して電源ユニットごとまとめてしまう
方法で解決したいと思います。
いつもの如く設計をFusion360で行いました。
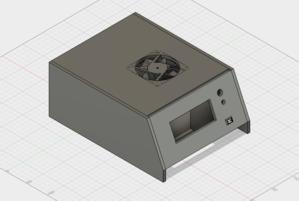
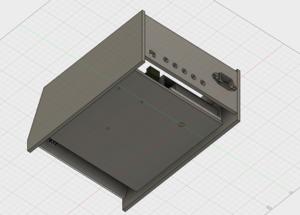
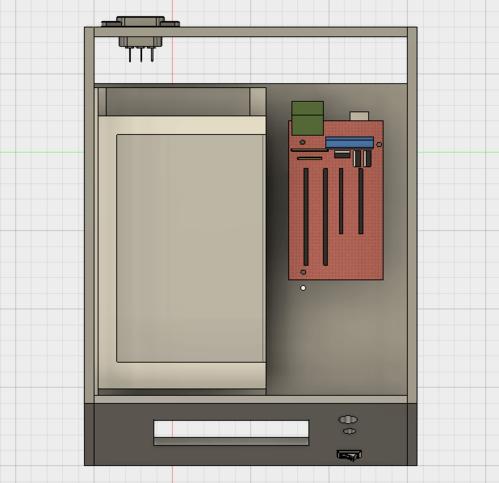
ボディはMDFで作成します。
板厚6mmで比較的大きめなものが、1枚108円でダイソーから購入できます。
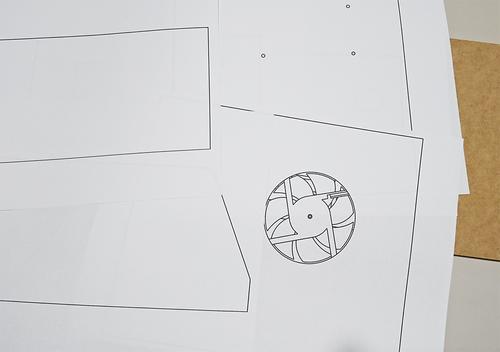
3Dデータを図面に起こして紙に印刷。
プロなら板に直接カットラインを引くのでしょうが、
私はケアレスミスが多いので、図面を直接貼り付けたほうが
間違いないのですわ。
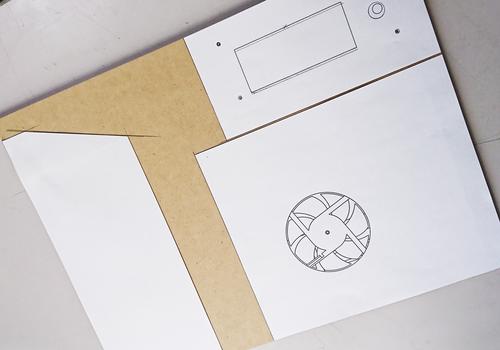
線を寸分違わずカット。板に粘着力の弱い両面テープで貼り付け。
紙に合わせて板をカットしていきます。全部で6面。
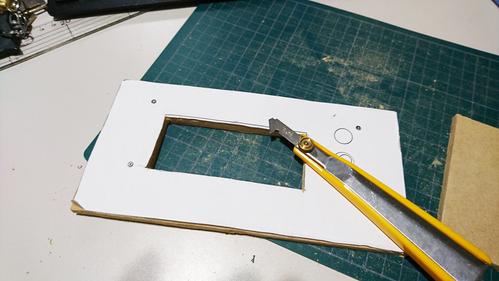
穴あけは糸鋸で開ければ早いのですが、
生憎手元になかったので、愛用のPカッターであけることに。
Pカッターと言えばアクリルやプラバンのカットに使うのが
一般的だと思いますが、実はもっと汎用性があるんです。
Pカッターは切るというより削りに近いので、
ちょっと複雑な形でも、削り切りで対応できます。
私は大きいホールソーが無いため、
今回はファンの形状に合わせて穴をあけるときにも
使いますので万能ですよ。
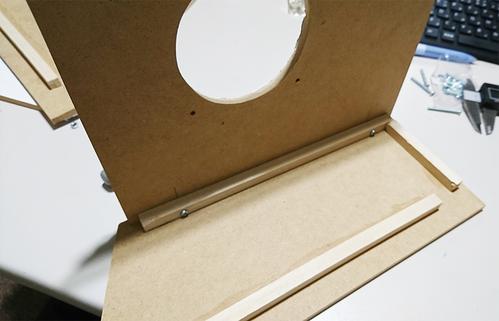
側面板に角棒を付けて、各板との接着強度を上げます。
天板の部分は開け閉めができるようにしないと不便なので、
接着ではなくネジで固定するようにしました。
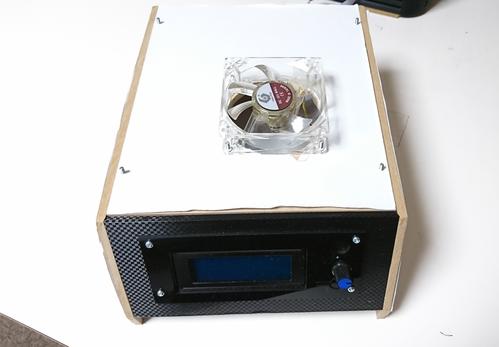
仮組み(未接着)
ファンは外側につけるのか、内側につけるのか思案中。
前面のパネルだけ先に作成してイメージを掴んでみました。
カーボン調のカッティングシートで雰囲気アップさせてます。
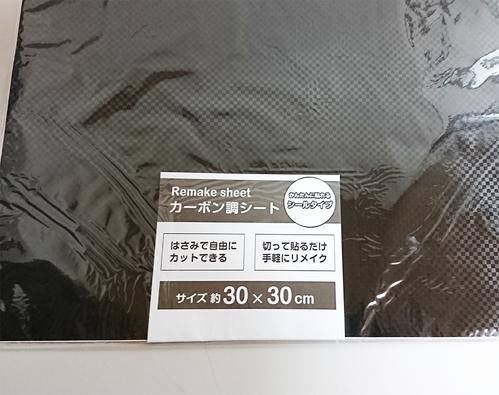
この段階でもパワースイッチの位置に悩んでいて、
前面につけるか、側面につけるか、背面につけるか・・・
中の配線の混み具合で決めることにしよう。。。
完成まで道のりが長いので話は一旦区切ります。
温度を上げると、その下にあるメインボードが熱せられる。
熱せられるとモータードライバのヒートシンク効率が下がる。
結果、脱調・暴走へと繋がってしまう。
このジレンマのせいで、ベッドの温度を80度までにして
ギリギリ動くラインを見極めているのですが、
印刷終了後、どうしても目視できるレベルの反りができてしまう。
小さいものを印刷して、良くて0.5mm、悪ければ1mmほど角が浮く。
やっぱり100度を超えたいよね。
ということで対策を考えれば
それはもうメインボードを天井に設置か
外に出すことしかありません。
私は、専用ケースを作成して電源ユニットごとまとめてしまう
方法で解決したいと思います。
いつもの如く設計をFusion360で行いました。
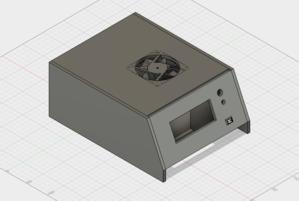
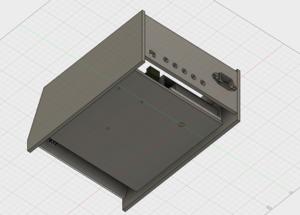
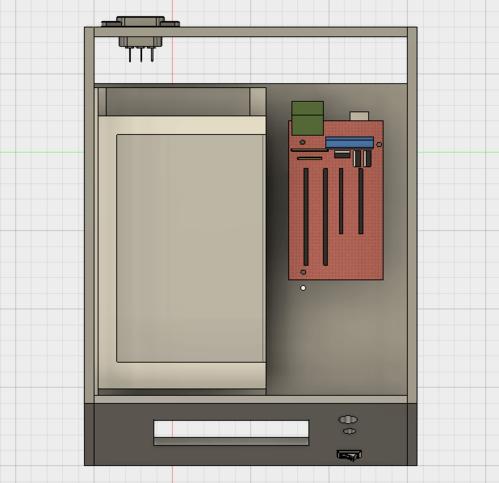
ボディはMDFで作成します。
板厚6mmで比較的大きめなものが、1枚108円でダイソーから購入できます。
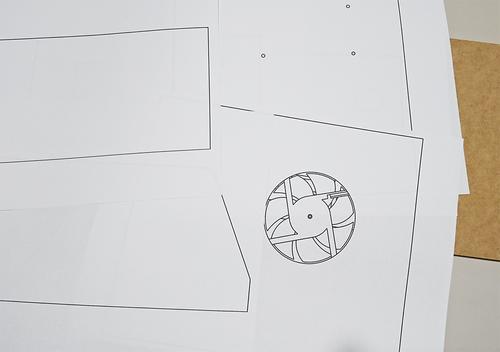
3Dデータを図面に起こして紙に印刷。
プロなら板に直接カットラインを引くのでしょうが、
私はケアレスミスが多いので、図面を直接貼り付けたほうが
間違いないのですわ。
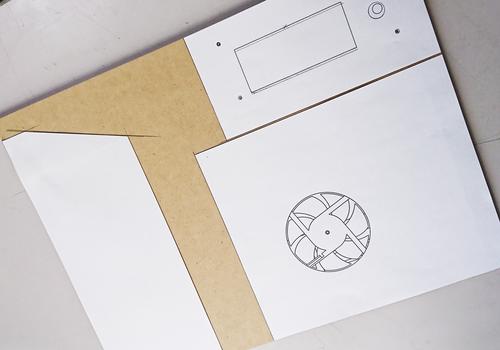
線を寸分違わずカット。板に粘着力の弱い両面テープで貼り付け。
紙に合わせて板をカットしていきます。全部で6面。
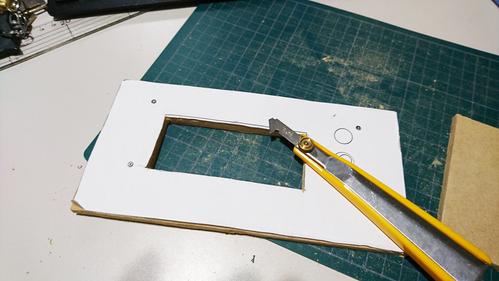
穴あけは糸鋸で開ければ早いのですが、
生憎手元になかったので、愛用のPカッターであけることに。
Pカッターと言えばアクリルやプラバンのカットに使うのが
一般的だと思いますが、実はもっと汎用性があるんです。
Pカッターは切るというより削りに近いので、
ちょっと複雑な形でも、削り切りで対応できます。
私は大きいホールソーが無いため、
今回はファンの形状に合わせて穴をあけるときにも
使いますので万能ですよ。
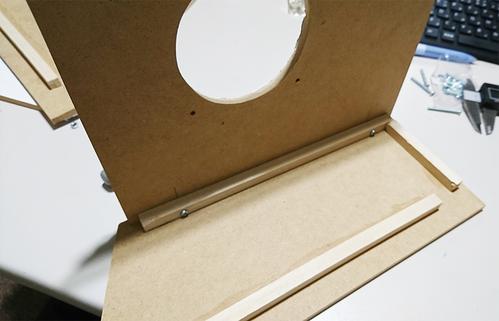
側面板に角棒を付けて、各板との接着強度を上げます。
天板の部分は開け閉めができるようにしないと不便なので、
接着ではなくネジで固定するようにしました。
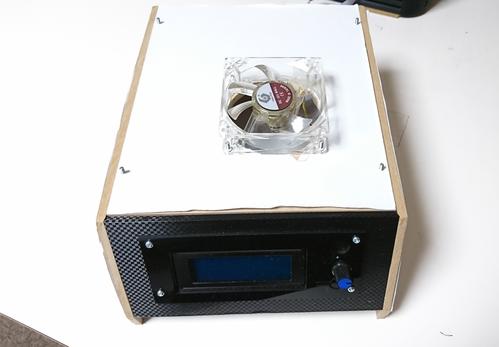
仮組み(未接着)
ファンは外側につけるのか、内側につけるのか思案中。
前面のパネルだけ先に作成してイメージを掴んでみました。
カーボン調のカッティングシートで雰囲気アップさせてます。
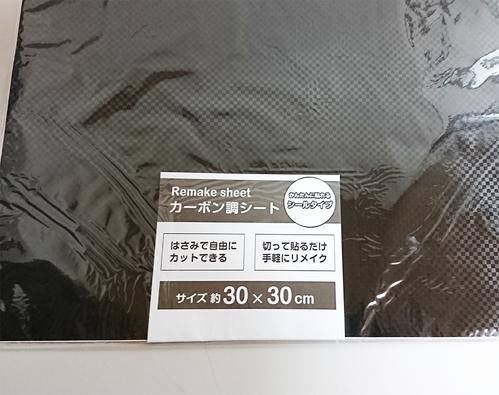
この段階でもパワースイッチの位置に悩んでいて、
前面につけるか、側面につけるか、背面につけるか・・・
中の配線の混み具合で決めることにしよう。。。
完成まで道のりが長いので話は一旦区切ります。
トラックバックURL
トラックバック一覧