Win10のFall Creators Updateでアプリが動かなくなる
2017.12.28
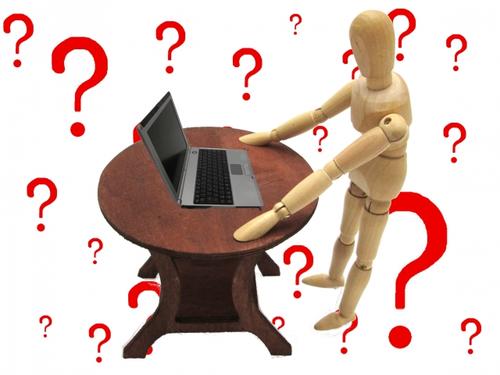
アップデートをしたらアプリが動かなくなってしまった!
という問い合わせを受けてクライアントに駆けつけたところ、
確かに動かない。なかなかお目にかかれない症状でした。
頻繁に使うExcelやWordを起動させようとすると、
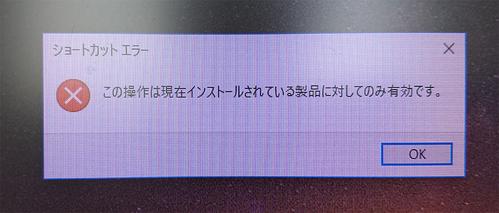
リンクがおかしいと怒られて、
直接EXEファイルを実行しても何も反応なし。
WinodwsLiveメールを起動してみると
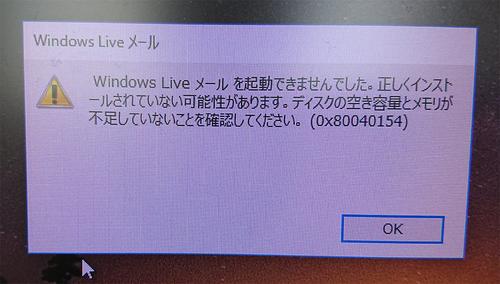
動きはするがいつもの画面までたどり着けず、
吐き出したメッセージはメモリエラー。
会計のソフトの定番、弥生を起動させてみると、
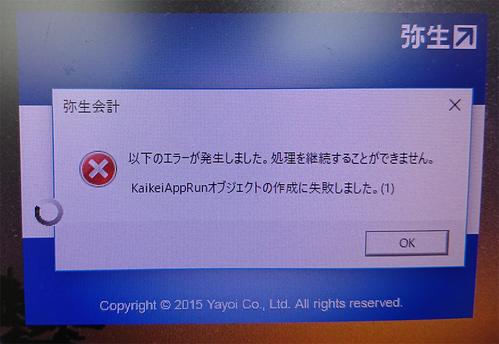
アプリも正常に動かないわ、データベースにも接続できないわで散々な有様に。
いろいろ試してみましたが、どうやらWin10で標準で組み込まれている
ツールやアプリ以外は軒並みアウトのようです。
つまりIEやEDGE等は問題なく動きます。
アップデートのログをみると正常に終了していると出ているが、
これはアプリ関連のレジストリ更新に失敗してるとしか思えない。
ネットで調べてみても同じ症状の話は見つからないので
簡単に解決できる特効薬を見つけるのは無理そう。
仕方ないので、アップデート前のWindowsに戻すことにしました。
確実に戻る保証は無いのでお客様の承諾を得てから、
必要なデータのバックアップをとり復元を実行。
時間にして15分。正常に復元できて事なきを得ました。
このような症状の場合、またFall Creators Updateが降ってきたら
同じことが起きる可能性があるので、
そのことを説明して今日は終わらせましたが、
Windows10のメジャーアップデートは
強制で行うのはやめてほしいものですね。
Kossel リビルド ボディフレーム編
2017.12.23
タイトル通りです。
金属パーツや拡張パーツを用いて再構築していきます。
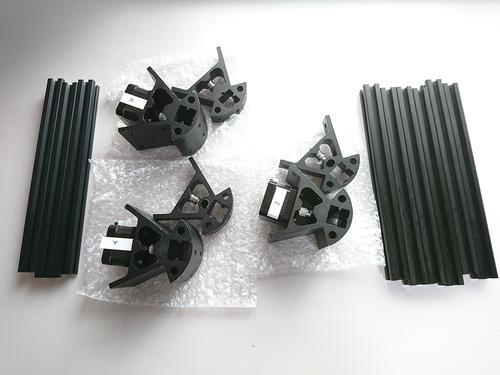
↑まずは、フレームの清掃。結構汚れてますね。
次に旧コーナーパーツについていたモーターとプーリーを移植。
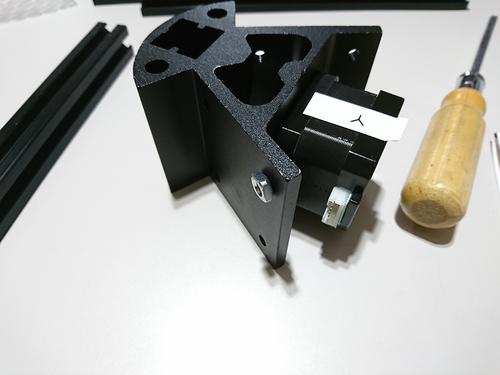
コーナーパーツにフレームを接続しようとしたら、トラブル発生。
既存のネジでは長さが足りない!
急遽10mmのネジを調達。
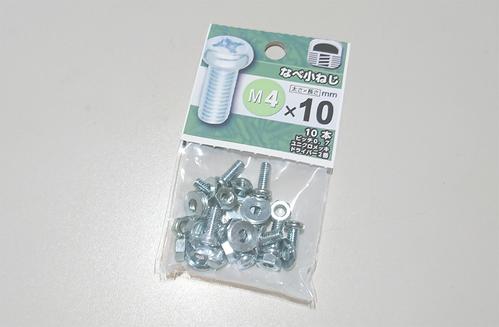
結構な本数が必要。ボトム4x2x3 トップ2x2x3で、計36本。
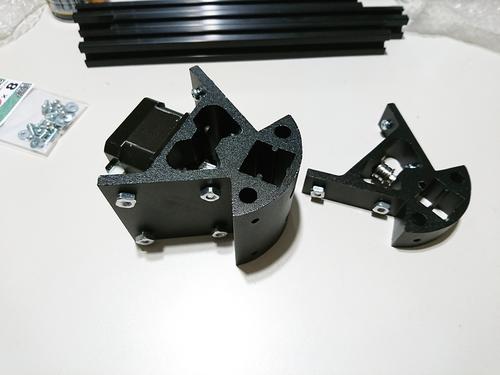
フレームを付ける前に、先にネジと四角ナットを軽くつけてから差し込むようにします。
これは前作と同じ工程ですね。
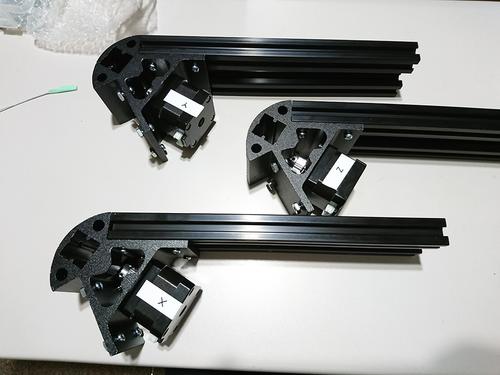
それぞれに片側だけ取り付けて、
手でフレームを掴むとカタカタ動くくらいのテンションでネジ軽く締めます。
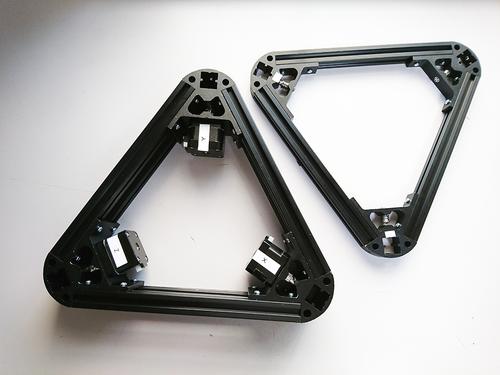
先程のネジ締めを軽めにしたことでフレームに遊びが出来ています。
それを利用してすべてを連結。
さっきの工程でネジ締めをキツキツにしてると簡単には連結できません。
連結が終わったら、水平をきっちり取りつつ、コーナーパーツとフレームとの間に
スキマが無い様にしっかり押さえ込みながらネジ締め。
これはなかなかしんどい作業です。
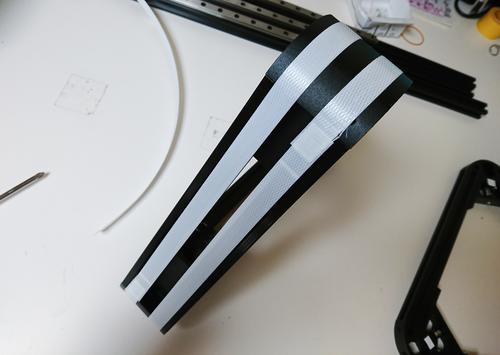
幸い、うちの事務所には半自動梱包機があるので、
バンドを強めに掛けて固定ができました。
隙間なくキッチリです。
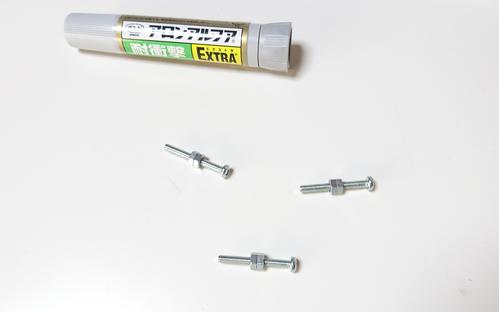
コーナーパーツが終わったところで、
エンドストップ用のピンを作成。
頭をカットして、カット先をダイスで切り直し。
回しやすいように中央にナットを2個ほど付けてますが、
1個でもよかったかな。
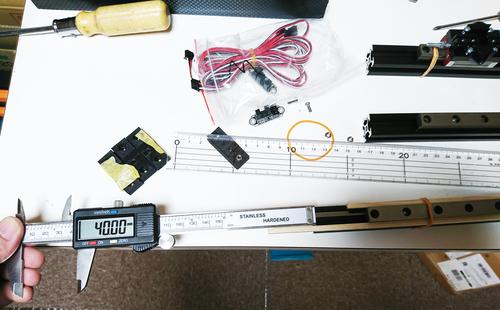
光学エンドストップを設置するスペースを確保するために
リニアレールを少し下へスライドさせる必要が出てきました。
ここはわかりやすいように40mmに設定しました。
スライドさせるには当然ネジを全部緩めるわけで、
そうなるとまたレールが斜めに傾いてしまう可能性があります。
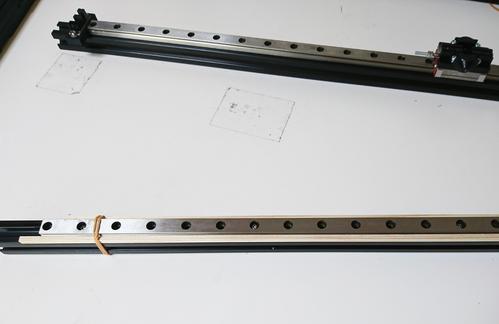
そうなることを防ぐために前にも行ったことが有りましたが、
4mmの角材を用いてキッチリセンターを出して固定します。
できれば金属の角材があれば良いのですが、
そんな都合のいいものはなかなか無いので木材で妥協です。
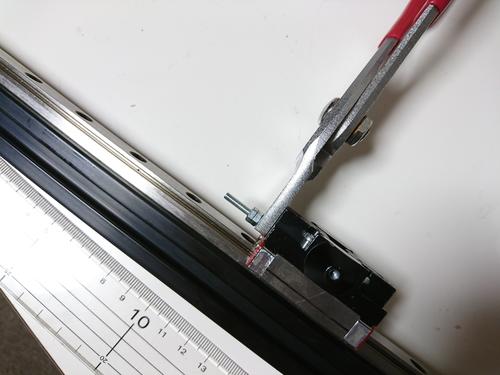
ピンを取り付けしてみると、キャリッジの穴が少し大きいせいで、
指で弾くとネジがすこしグラつきます。これでは不安定極まりないので
動きを止めるためにネジ止め剤で一旦留めます。
今後は、光学エンドストップなので、ブレさえなければ、
ピンに力が加わるわけでもないので
それほど神経質になることもないでしょう。
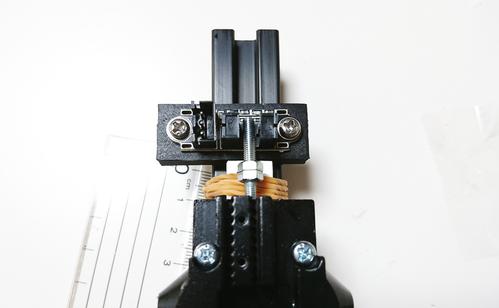
光学エンドストップを取り付けてみました。
ピンの位置がセンサー内でキレイに収まっています。
台座は設計通りで造形エラーは無しでした(๑´ڡ`๑)
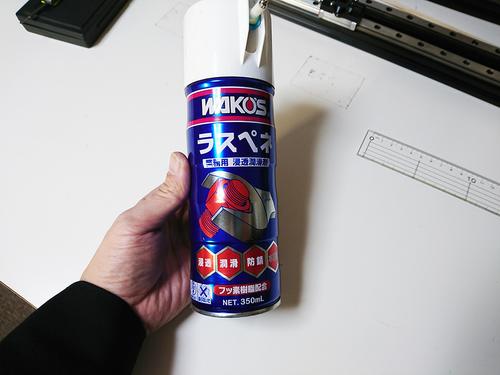
スライダーのほうにも手をいれます。
レールから外して、ボールベアリング部に油を直接挿します。
556だと垂れが大きく、全体に行き渡らないきがしたので
泡状に塗布できて浸透率が高い業務用ラスペネを使いました。
最近人気急上昇のベルハンマーもあるのですが、
先の細い油差しがなかったので今回は見送りです。

で、先日ふっ飛ばしてしまったベアリングですが、
ミスミから3日で到着しました。
Aliexpressの注文に慣れてしまったせいか
異様に早く感じます。毒されてるなぁ(;´Д`)
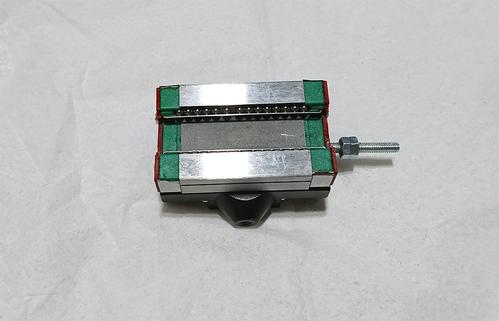
早速組み込んで見ました。
使ったボールは、片側33個、計66個という結果です。
新品のボールを使ってもスキマはできるので、
このスキマはボールの摩耗ではなくて、仕様なのですね。
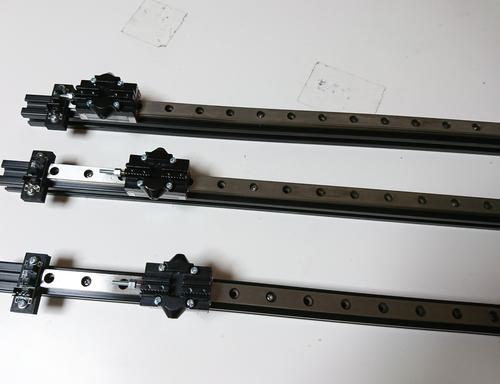
これでレール部分は完成。
ラスペネを塗布しているせいか、全てのレールが滑らかに動いています。
ボールベアリングを交換したレールも、滑らかに動いてくれています。
逆に遊びが減って動きがよりシャープな感じがする。
いやプラシーボ効果かな。
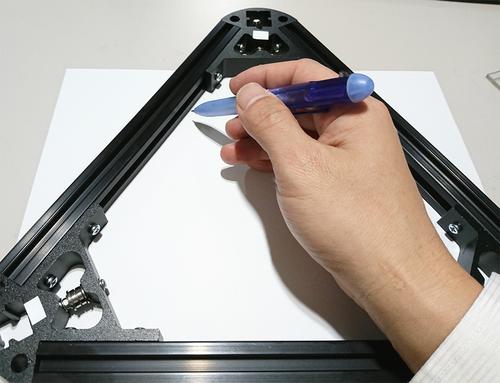
そうそう、フレームを組み上げる前に、やっていく作業が有りました。
それは、ヒートベッドの下に敷く板の型をとること。
ヒートベッドの下が大きい空間になってしまっては
温度上昇がなかなか進みませんので、
板を敷いて熱を逃がさない作戦です。
いつもなら3DCADから図面を引くところですが、
ここは精度が必要ないので、ペンで内枠の形を型どりました。
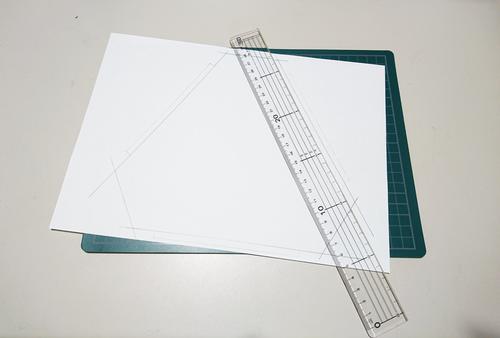
あやふやな線を正確なものに書き換えます。
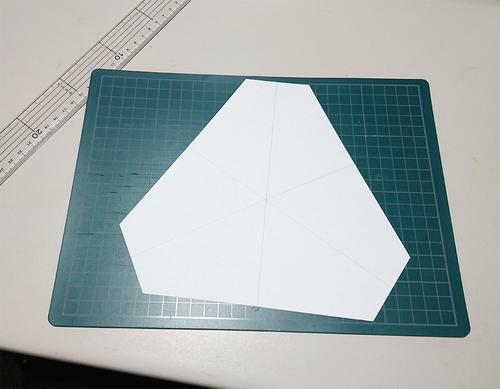
カットして型紙完成。中央に配線用の穴も開けるので中心も出しておきます。
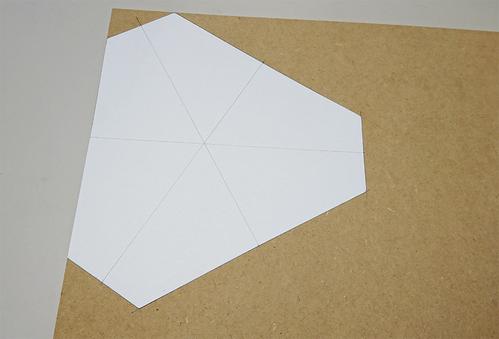
MDFに貼り付け。軽く板にもラインを引いておきます。
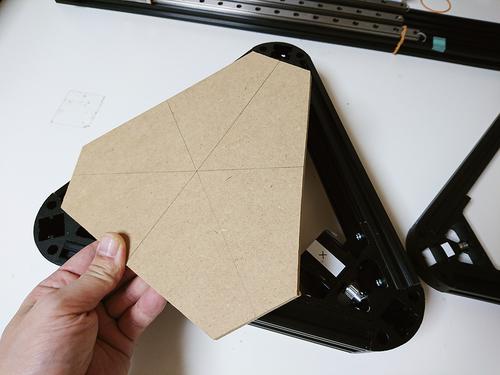
ノコギリでカット。線通りに引くとキチキチになりかねないのですが、
ノコギリの刃自体が2mmの厚みがあるので、
線をセンターにして切ると少しだけ小さくなるので丁度良くなります。
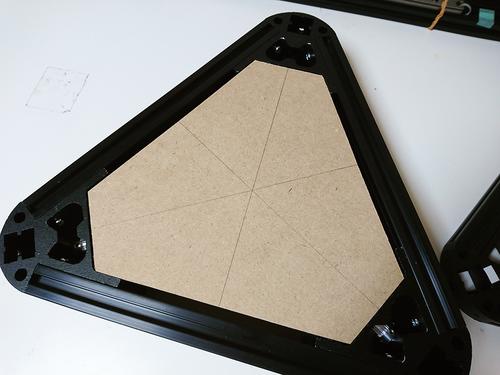
うん、ピッタリ。
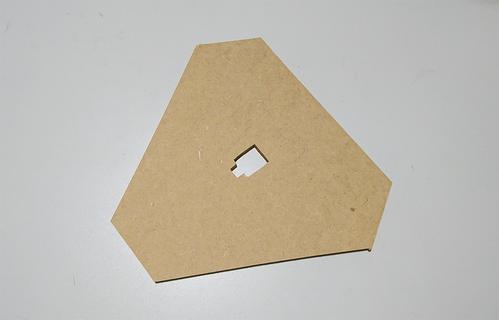
ヒートベッドのハンダ部分&配線部分に接触する箇所に穴を開けます。
穴は小さく角が多いので彫刻刀で開けました。
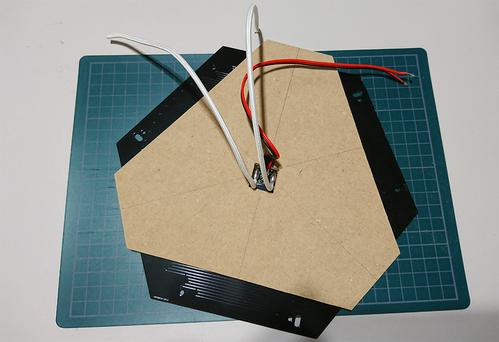
最小限の穴サイズ。
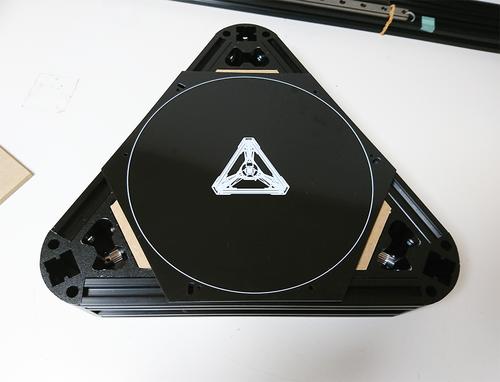
固定イメージはこんな感じ。
MDFが見えてしまう部分は熱せられるわけじゃないし、
ケースに使ったカッティングシートを貼ろうかな。
まぁ、あとから考えよう。
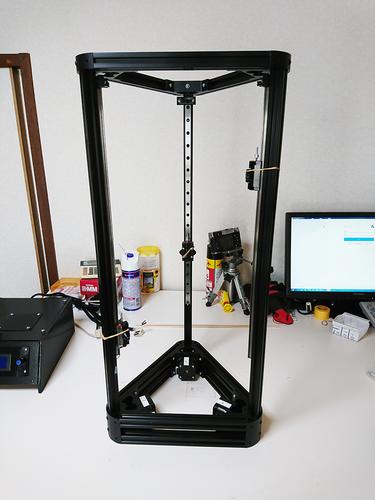
最後は柱を連結させて完成。
ここの段階でフレームの強固さがハッキリわかります。
重さがあるので安定感は当然増していますが、
それ以上に剛性が明らかに高まっている。
手で押しても全くブレません。
これは印刷速度を上げた時の造形に期待が持てますね。
金属パーツや拡張パーツを用いて再構築していきます。
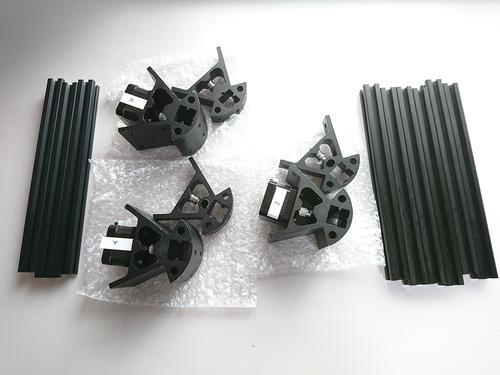
↑まずは、フレームの清掃。結構汚れてますね。
次に旧コーナーパーツについていたモーターとプーリーを移植。
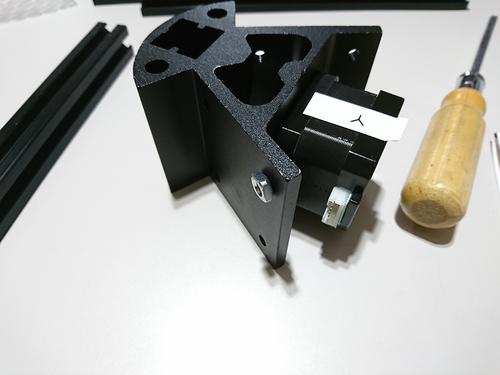
コーナーパーツにフレームを接続しようとしたら、トラブル発生。
既存のネジでは長さが足りない!
急遽10mmのネジを調達。
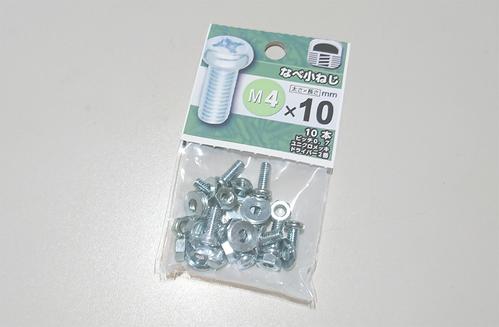
結構な本数が必要。ボトム4x2x3 トップ2x2x3で、計36本。
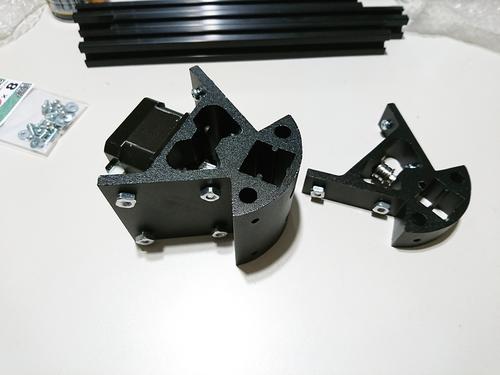
フレームを付ける前に、先にネジと四角ナットを軽くつけてから差し込むようにします。
これは前作と同じ工程ですね。
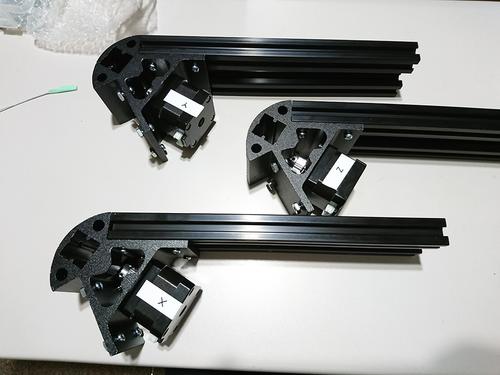
それぞれに片側だけ取り付けて、
手でフレームを掴むとカタカタ動くくらいのテンションでネジ軽く締めます。
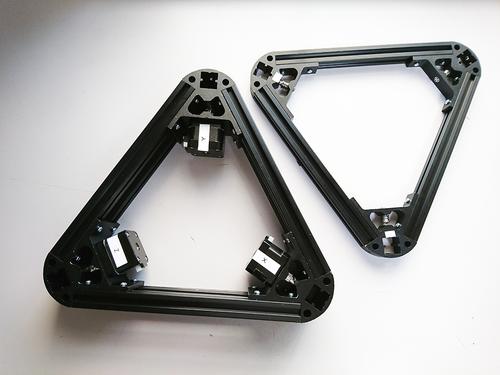
先程のネジ締めを軽めにしたことでフレームに遊びが出来ています。
それを利用してすべてを連結。
さっきの工程でネジ締めをキツキツにしてると簡単には連結できません。
連結が終わったら、水平をきっちり取りつつ、コーナーパーツとフレームとの間に
スキマが無い様にしっかり押さえ込みながらネジ締め。
これはなかなかしんどい作業です。
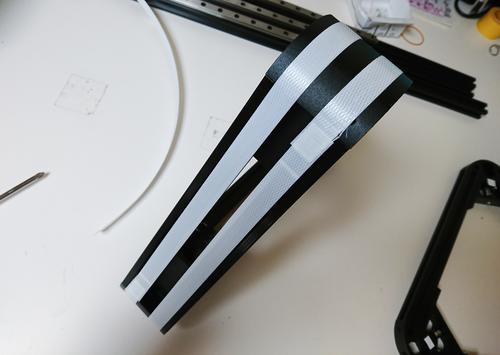
幸い、うちの事務所には半自動梱包機があるので、
バンドを強めに掛けて固定ができました。
隙間なくキッチリです。
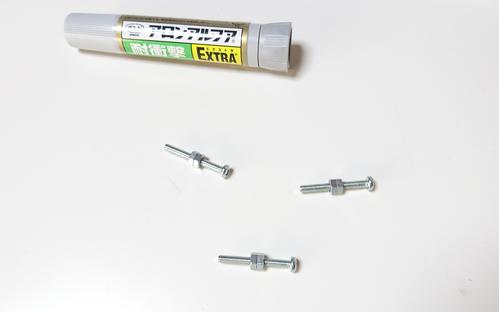
コーナーパーツが終わったところで、
エンドストップ用のピンを作成。
頭をカットして、カット先をダイスで切り直し。
回しやすいように中央にナットを2個ほど付けてますが、
1個でもよかったかな。
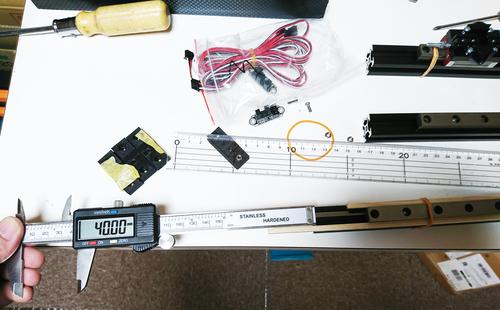
光学エンドストップを設置するスペースを確保するために
リニアレールを少し下へスライドさせる必要が出てきました。
ここはわかりやすいように40mmに設定しました。
スライドさせるには当然ネジを全部緩めるわけで、
そうなるとまたレールが斜めに傾いてしまう可能性があります。
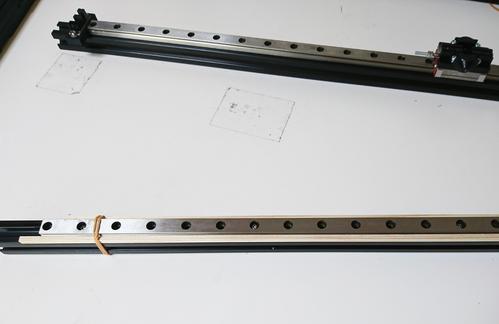
そうなることを防ぐために前にも行ったことが有りましたが、
4mmの角材を用いてキッチリセンターを出して固定します。
できれば金属の角材があれば良いのですが、
そんな都合のいいものはなかなか無いので木材で妥協です。
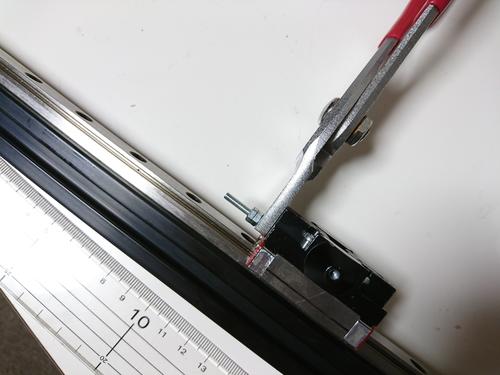
ピンを取り付けしてみると、キャリッジの穴が少し大きいせいで、
指で弾くとネジがすこしグラつきます。これでは不安定極まりないので
動きを止めるためにネジ止め剤で一旦留めます。
今後は、光学エンドストップなので、ブレさえなければ、
ピンに力が加わるわけでもないので
それほど神経質になることもないでしょう。
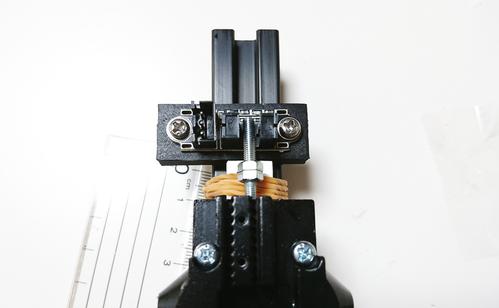
光学エンドストップを取り付けてみました。
ピンの位置がセンサー内でキレイに収まっています。
台座は設計通りで造形エラーは無しでした(๑´ڡ`๑)
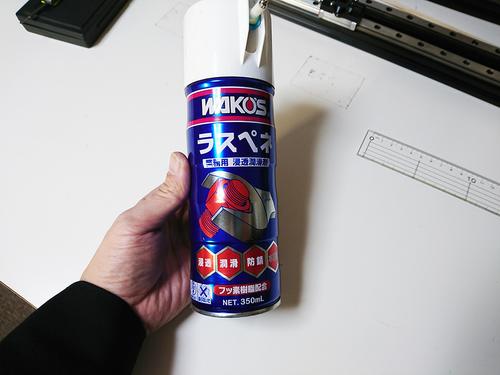
スライダーのほうにも手をいれます。
レールから外して、ボールベアリング部に油を直接挿します。
556だと垂れが大きく、全体に行き渡らないきがしたので
泡状に塗布できて浸透率が高い業務用ラスペネを使いました。
最近人気急上昇のベルハンマーもあるのですが、
先の細い油差しがなかったので今回は見送りです。

で、先日ふっ飛ばしてしまったベアリングですが、
ミスミから3日で到着しました。
Aliexpressの注文に慣れてしまったせいか
異様に早く感じます。毒されてるなぁ(;´Д`)
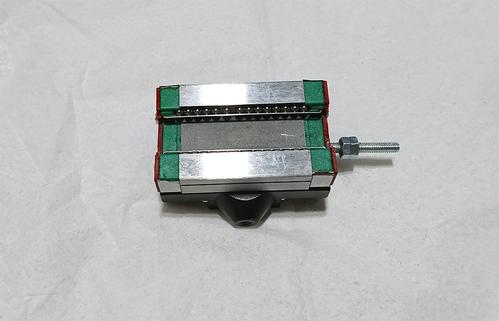
早速組み込んで見ました。
使ったボールは、片側33個、計66個という結果です。
新品のボールを使ってもスキマはできるので、
このスキマはボールの摩耗ではなくて、仕様なのですね。
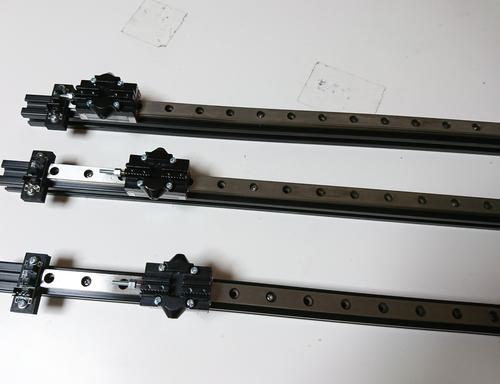
これでレール部分は完成。
ラスペネを塗布しているせいか、全てのレールが滑らかに動いています。
ボールベアリングを交換したレールも、滑らかに動いてくれています。
逆に遊びが減って動きがよりシャープな感じがする。
いやプラシーボ効果かな。
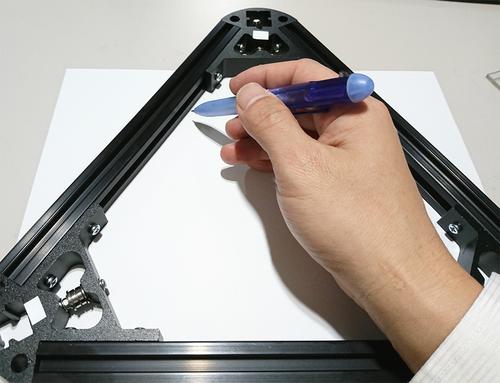
そうそう、フレームを組み上げる前に、やっていく作業が有りました。
それは、ヒートベッドの下に敷く板の型をとること。
ヒートベッドの下が大きい空間になってしまっては
温度上昇がなかなか進みませんので、
板を敷いて熱を逃がさない作戦です。
いつもなら3DCADから図面を引くところですが、
ここは精度が必要ないので、ペンで内枠の形を型どりました。
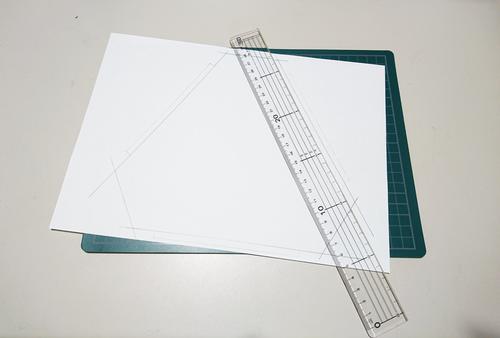
あやふやな線を正確なものに書き換えます。
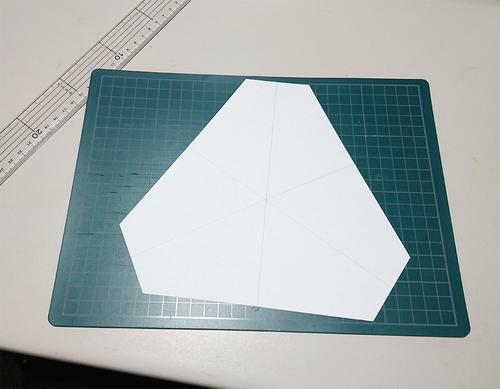
カットして型紙完成。中央に配線用の穴も開けるので中心も出しておきます。
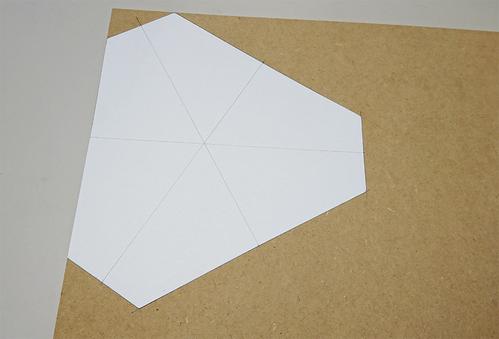
MDFに貼り付け。軽く板にもラインを引いておきます。
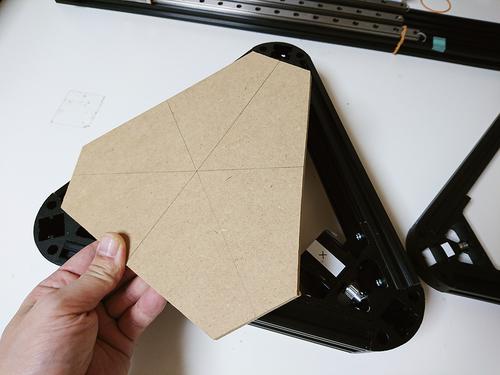
ノコギリでカット。線通りに引くとキチキチになりかねないのですが、
ノコギリの刃自体が2mmの厚みがあるので、
線をセンターにして切ると少しだけ小さくなるので丁度良くなります。
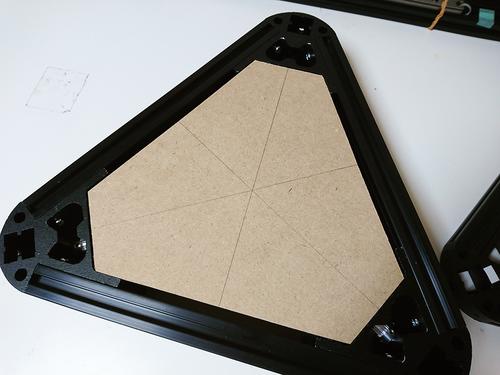
うん、ピッタリ。
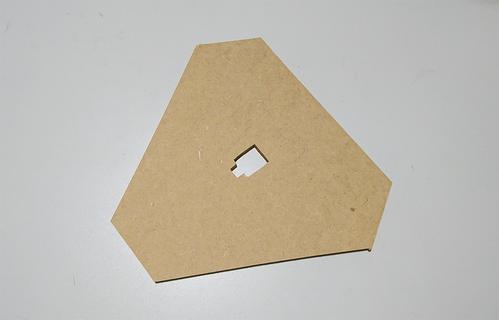
ヒートベッドのハンダ部分&配線部分に接触する箇所に穴を開けます。
穴は小さく角が多いので彫刻刀で開けました。
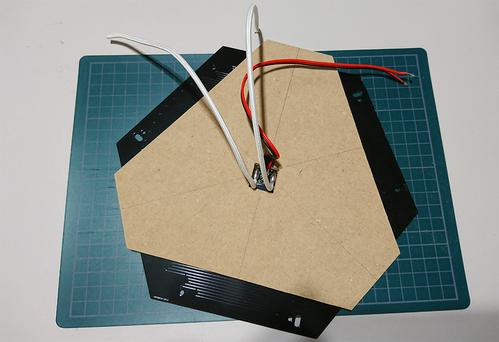
最小限の穴サイズ。
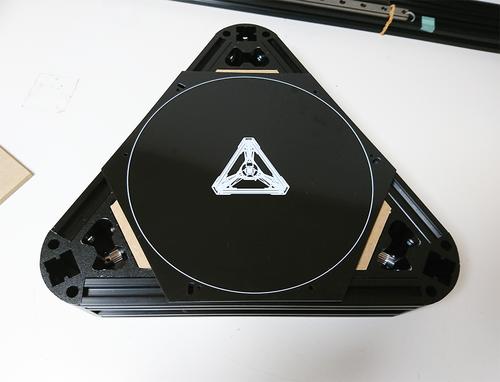
固定イメージはこんな感じ。
MDFが見えてしまう部分は熱せられるわけじゃないし、
ケースに使ったカッティングシートを貼ろうかな。
まぁ、あとから考えよう。
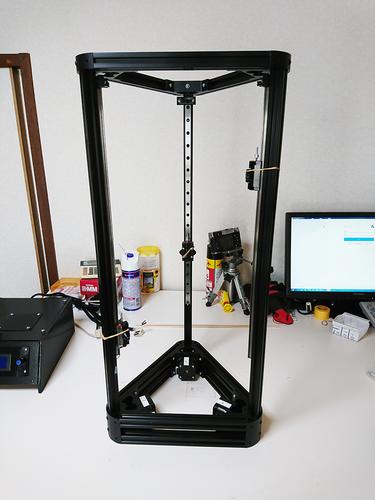
最後は柱を連結させて完成。
ここの段階でフレームの強固さがハッキリわかります。
重さがあるので安定感は当然増していますが、
それ以上に剛性が明らかに高まっている。
手で押しても全くブレません。
これは印刷速度を上げた時の造形に期待が持てますね。
Kossel Mini 解体
2017.12.20
先日メインボードケースを作成するときに、
Arduinoを取り外したところまでいきましたが、
今回は完全解体です。
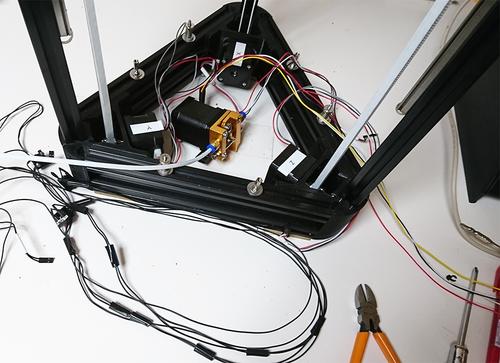
ここまで15分。組み立てるのに時間かかったのにバラすのはあっという間です。
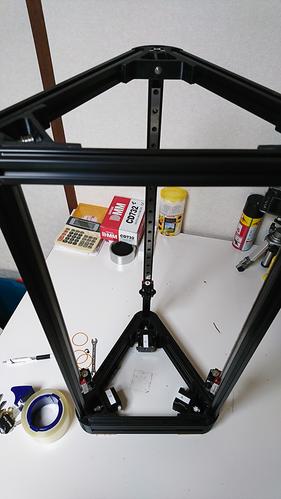
モーターとレール以外のパーツを完全に除去しました。
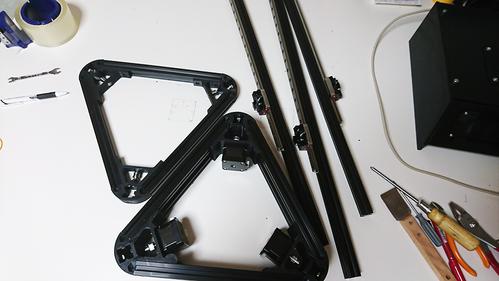
柱を外して、トップとボトムに分解。
その際に悲劇が ΣΣ(゚д゚lll)ガガーン!!
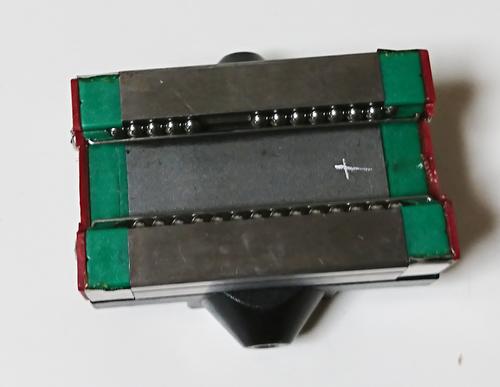
レールからキャリッジがハズレてしまい、
ボールベアリングが部屋中にばら撒かれてしまいました。
必至に掻き集めましたが、どうにも3個ほど足りない。
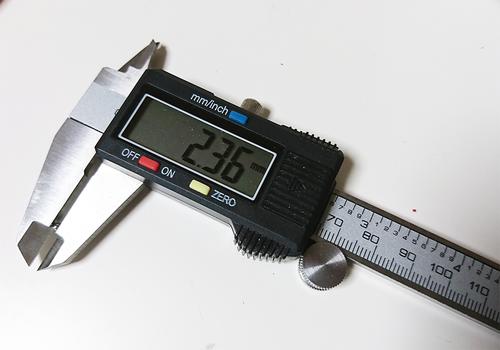
発注しなくきゃどうにもならないので
ベアリングのサイズを調べてみます。
0.02mmほど違いますが、微妙に摩耗してることも考慮して
これは3/32インチサイズで間違いないと思います。
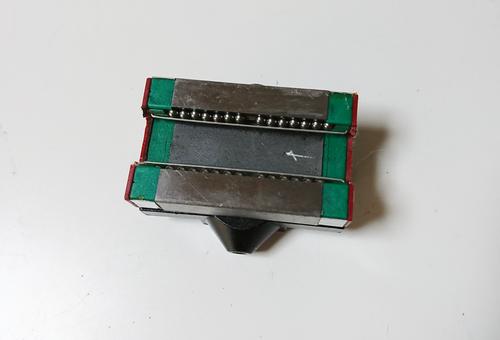
↑念のためベアリングが飛んでいないキャリッジを外して
正常な状態というものを確認してみました。
どうにも1個分のスペースが足りないように見えます。
試しにバラけたベアリングを填めてみようとしてみますが、
キレイに収まりませんね・・ これはスペースが開いていて正解なのか・・
さすが中国製品。
まさか、この分だけボールが摩耗ってことないよね(;´Д`)
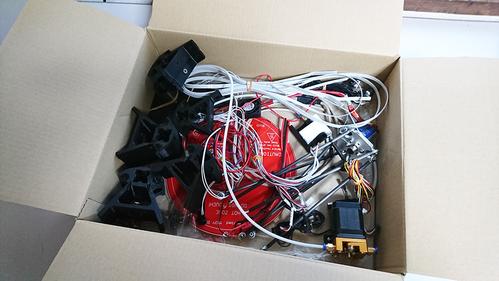
物が届くまではキャリッジは手がつけられないので
他を解体。トップとボトムからアルミフレームも外して、
完全にバラバラになったKossel君。
まとめると意外とコンパクトなんだなぁ・・
Arduinoを取り外したところまでいきましたが、
今回は完全解体です。
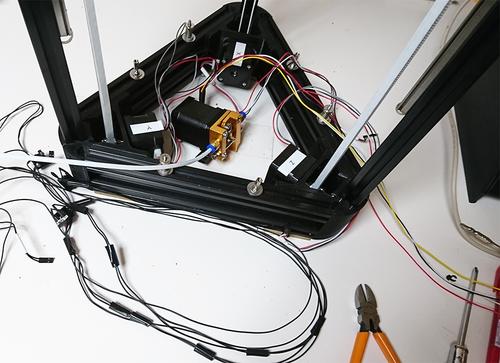
ここまで15分。組み立てるのに時間かかったのにバラすのはあっという間です。
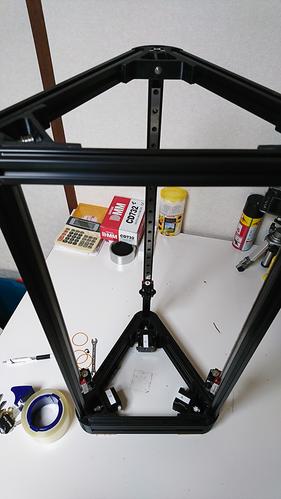
モーターとレール以外のパーツを完全に除去しました。
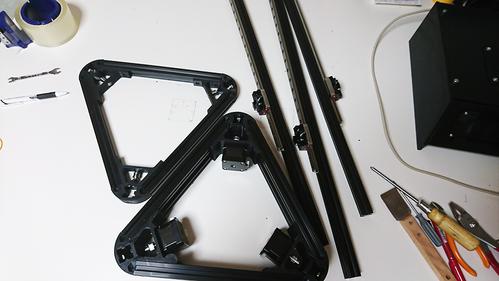
柱を外して、トップとボトムに分解。
その際に悲劇が ΣΣ(゚д゚lll)ガガーン!!
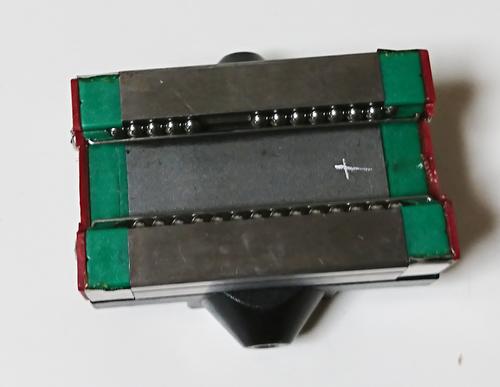
レールからキャリッジがハズレてしまい、
ボールベアリングが部屋中にばら撒かれてしまいました。
必至に掻き集めましたが、どうにも3個ほど足りない。
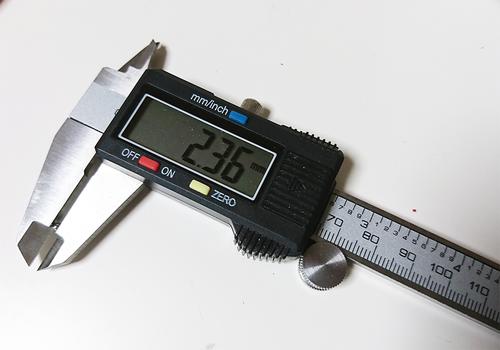
発注しなくきゃどうにもならないので
ベアリングのサイズを調べてみます。
0.02mmほど違いますが、微妙に摩耗してることも考慮して
これは3/32インチサイズで間違いないと思います。
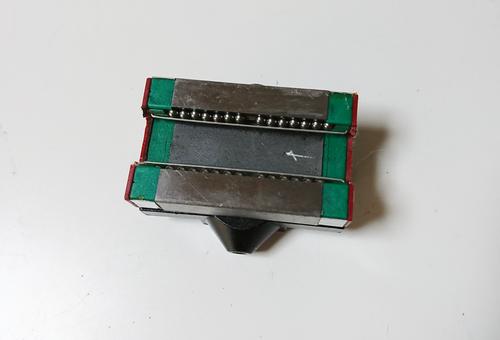
↑念のためベアリングが飛んでいないキャリッジを外して
正常な状態というものを確認してみました。
どうにも1個分のスペースが足りないように見えます。
試しにバラけたベアリングを填めてみようとしてみますが、
キレイに収まりませんね・・ これはスペースが開いていて正解なのか・・
さすが中国製品。
まさか、この分だけボールが摩耗ってことないよね(;´Д`)
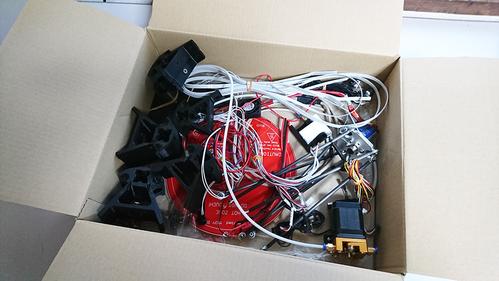
物が届くまではキャリッジは手がつけられないので
他を解体。トップとボトムからアルミフレームも外して、
完全にバラバラになったKossel君。
まとめると意外とコンパクトなんだなぁ・・